Jeremy Dunne
Composite Filament Winding
Starting in summer 2019, I began programming and upgrading a filament winder to make fiberglass body tubes and nose cones. I wrote software to enable the winding of any parametric shape, and successfully demonstrated the viability of my system with a supersonic test vehicle, nick-named Speed Demon in the spring of 2020.
Mechanics
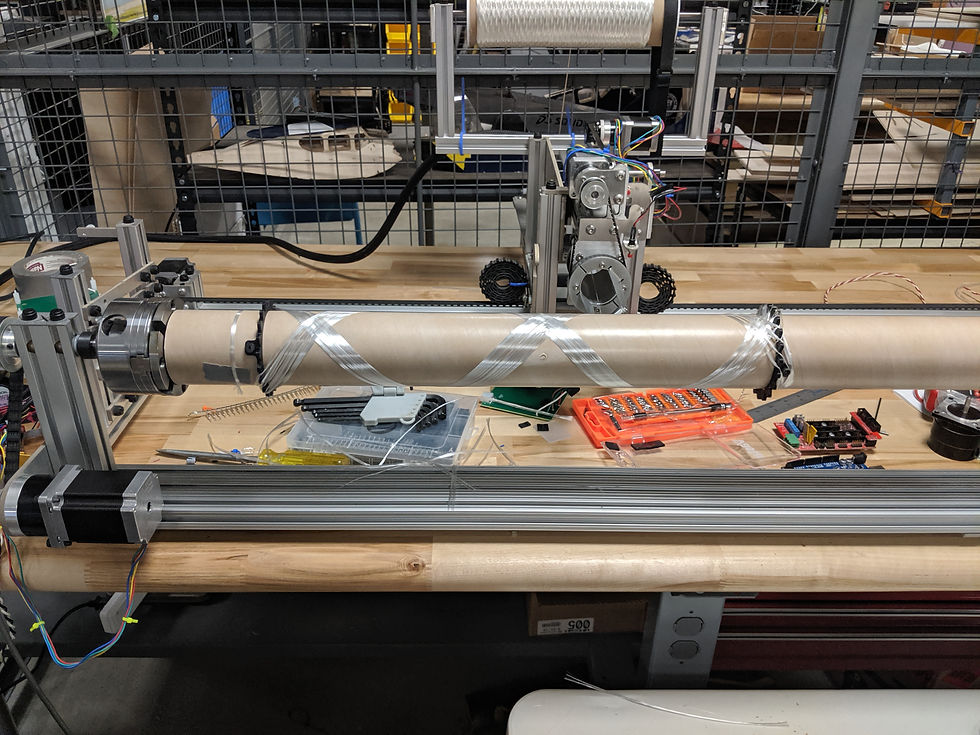
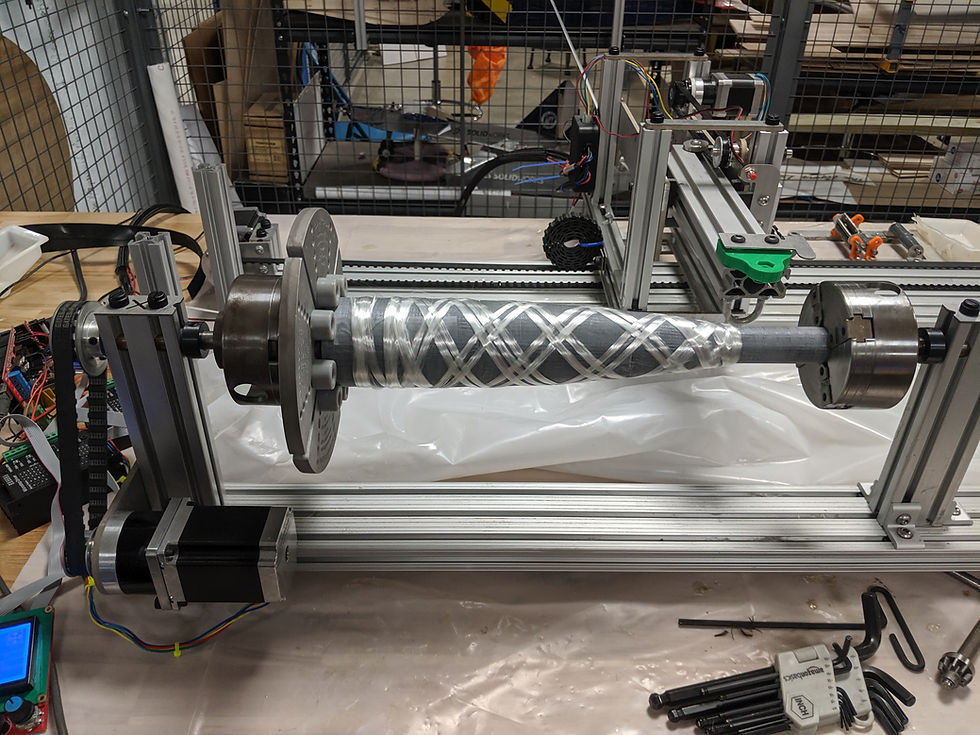
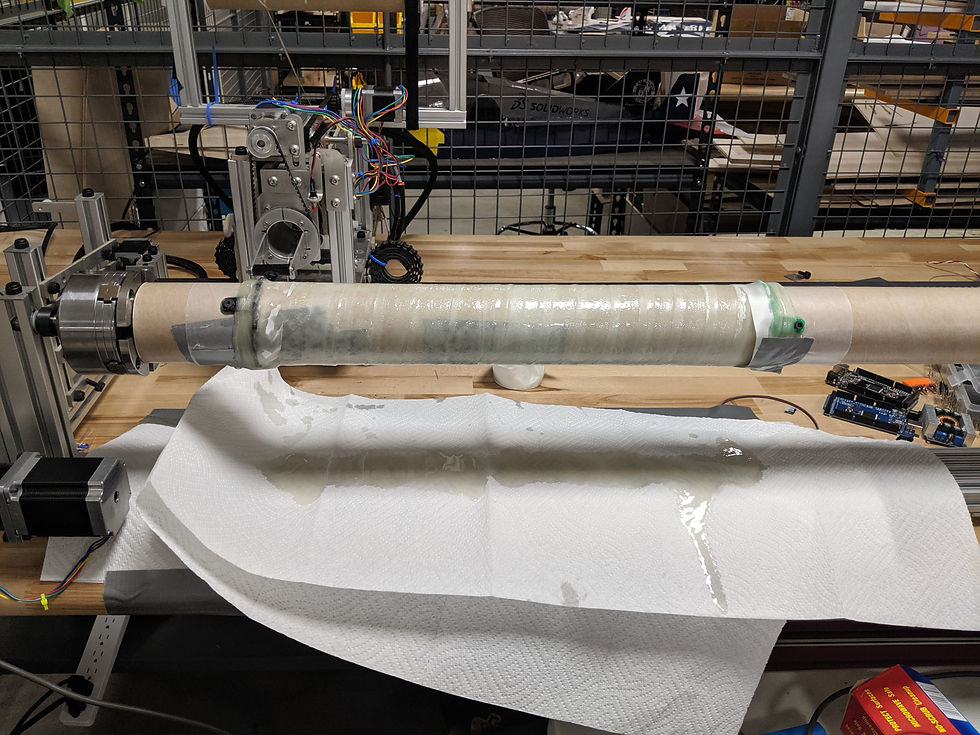
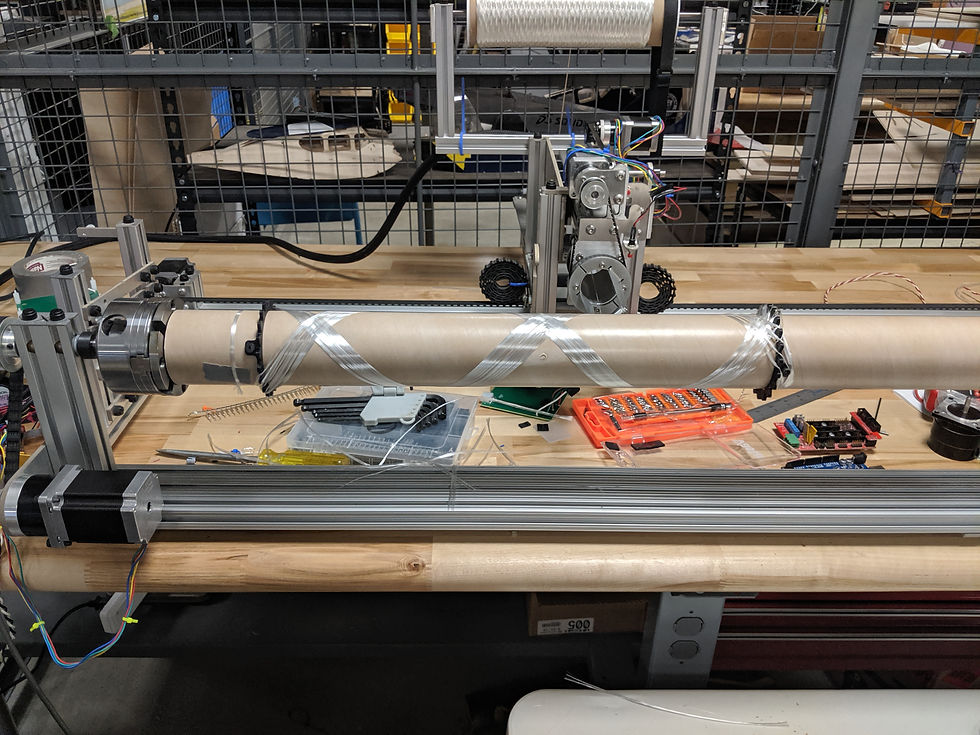
The Filament Winder is based on the X-Winder with upgrades I have performed to increase the capabilities. The largest upgrade performed included allowing up to eight fiberglass filaments to be wound down simultaneously.
The design uses two main axes, a rotational and a linear axis to wind on a mandrel.
Electronics
To increase the capabilities of the winder, I replaced the standard controller with a salvaged 3D Printer controller that interpreted direct GCode.
To create the GCode commands that would run on the controller, I wrote a program in Python to generate the winding patterns. This program is can generate winding patterns for any concave parametric shape, including body tubes, nose cones, and transitions.
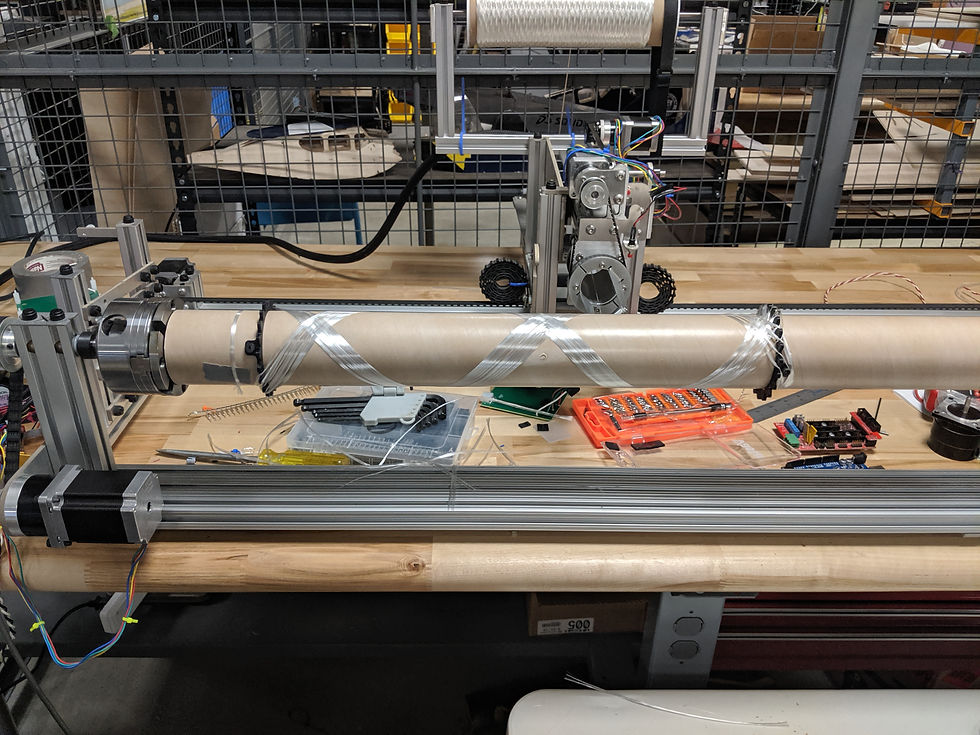


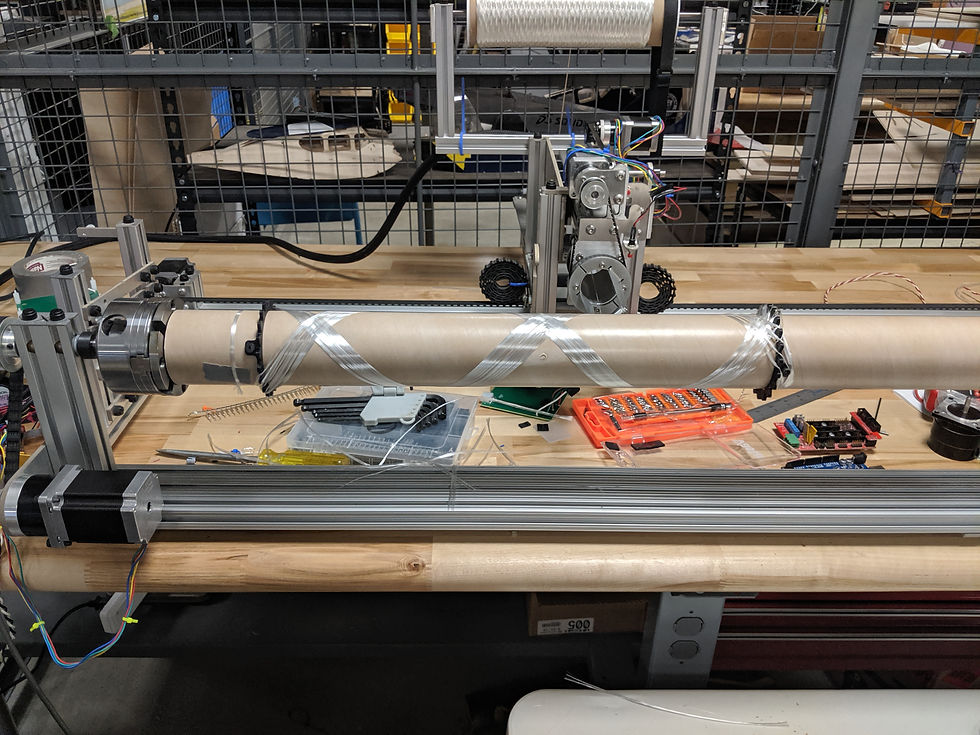
Testing & Validation
After creating and running several test tubes through the winder, I decided to test the quality and capabilities of the winded objects. To do this, I design, constructed, and built a supersonic test rocket, Speed Demon, built solely from tubes and nosecones wound on this winder. This rocket has been launched twice, achieving a max velocity of mach 0.98 (close, but not quite mach 1), validating the strength and capabilities of the modified winder.

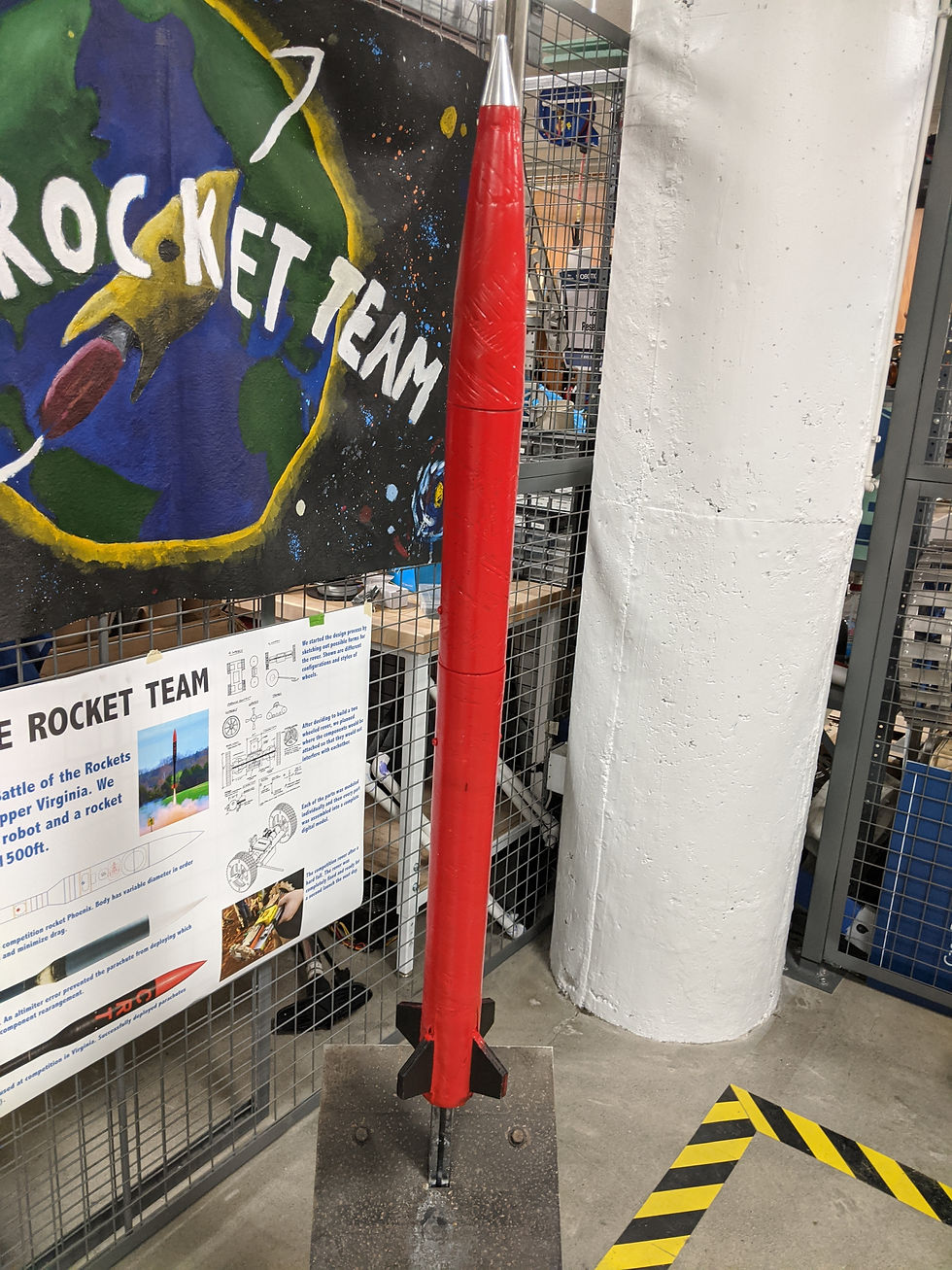


Skills Demonstrated
-
Mechanical Design
-
Solidworks
-
GCode
-
CAM
-
Manufacturing (Manual & Water-jet Cutting)
-
Programming (Python)
-
Control Hardware